Concept Statement
Centrifugal pumps running on normal AC power supply are very common, fairly efficient and most importantly they are locally available from wide range of manufacturers. Their use and operation is more or less hasslefree, they are easily serviceable at nearby workshops and pricewise also they are affordable. These points are specifically important in comparison to a classical solar pump system that is available in market these days, and which potentially uses a BLDC 3 phase DC motor/pump with permanent magnets and all stainless steel body.
These standard AC pumps are available in 0.5 HP to 10s of HP of power rating, able to run on single phase (220V) or three phase (415V) AC power supply and available in formats like monoblock pumpset, openwell submersible and borewell submersible pumps.
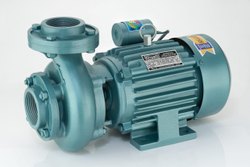
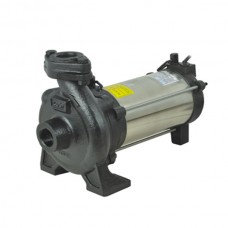
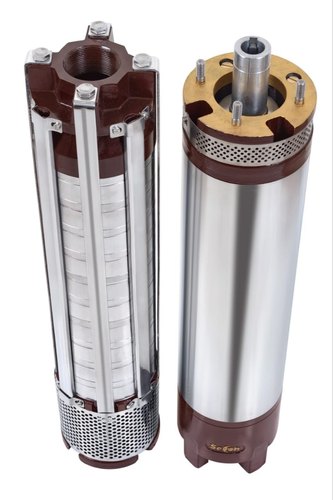
This article discusses the use of such standard AC pumps using Solar Panels as the source of electricity.
Since solar panels generate DC voltage, it is important to have some mechanism or device to convert the DC electricity from the panels to AC power so that the pump can run on it.
A standard AC motor consumes large amounts of current during startup for a few seconds, this current can be 2 to 6 times of the normal operating current at full load. On the other hand solar panels are a current limited source of power i.e. the current output available from a given solar panel is limited by the size of panel. This means that the solar panels which would be sized and selected to meet the current requirements of the pump at normal operating load are not going to be able to start the pump in normal or traditional manner. Some kind of soft start approach is needed.
Also based on sunlight available over the day time, the output voltage, current and power from solar panels is going to vary, this needs to be maximized by making the pump run at various voltage and/or AC frequency. The standard AC motor which is expected to operate at 50 Hz power supply, can actually be made to run over a range of supply frequency (35 to 55 Hz) without any significant side effects. In this range of frequency, the output power of the motor varies almost linearly and this inherent feature can be used to match the solar panel output with the pump-motor power requirements.
All the above leads to a solution which has to be based on some sort of electronics to support following features.
- DC to AC conversion
- Soft start or gradually increasing voltage during startup
- Output voltage and frequency modulation to optimize the power generation from the solar panels.
For 1 and 2 above there already exists a robust industrial device called Variable Frequency Drive (VFD). VFDs are often used in various industries to control the load and/or speed of standard AC motors which drive the heavy plant and machinery.
Most VFDs allow AC (single or three phase) or DC power supply as input and generate three phase AC power as output.

Internally the input AC power supply is first rectified to DC, that is what makes VFD suitable to run with Solar Panels. Then a microcontroller based circuitry drives a set of power transistors (IGBT or MOSFETs) to achieve DC to AC conversion with a SPWM (sinusoidal pulse width modulation) technique.
The output power is a sine wave with a configurable mains frequency (10 to 60 Hz as an example) but laden with spikes or chopped waveform with a carrier frequency of a few kilo-Hz. This is acceptable for standard AC motors, or rather the carrier frequency used in commercially available VFDs is optimized to keep the motors healthy and not to generate any ill-effects, especially high frequency harmonics.
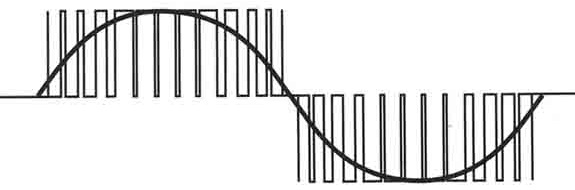
The same waveform as explained and shown above, is generated in all the three phases of the output, but appropriately phase shifted by 120 degrees from each other. That makes a nice power source for a three phase AC motor.
During startup the VFD outputs a lower frequency of say 10 Hz and correspondingly lower pulse width (effectively a reduced AC voltage at the output). It is then gradually increased over a period of 5 to 15 seconds to normal operating frequency of 50 Hz. That is how a soft start is implemented.
VFDs have a simple and basic keypad with start, stop, menu buttons. Keypad permits setting of various configurable parameters, and also displays the operating status/errors if any.
Connectivity with external controlls is also provided, which allows dynamically setting the output frequency and voltage, external start and stop commands etc.
A fewer brands of VFDs have started manufacturing VFDs with additional features as below.
- Customized phaseshift of 90/110 degrees (instead of 120) between the three output phases, to emulate the 3 wire power supply of a single phase capacitor run motor.
- Changes to output frequency at runtime based on an inbuilt MPPT (maximum power point tracking) algorithm, essential for solar panels.
Test Results
With the concept explained so far as above, we have carried out a few real life tests using a VFD and borewell submersible pump.
Equipment used is listed below
- FRECON Make Solar VFD, model number FR150T – 2S – 2.2B -H, this accepts single phase AC input or DC input and gives out 3 phase 220 VAC. Has configuration settings to connect a single phase motor across the three U V W output terminals, and also has a MPPT algorithm in-built into it. It is not a Make In India brand but has ample presence of local dealer network in India. Build wise seems a good robust build.
- Kirloskar make borewell submersible pump model Jalaraj KP4-1009 with 10 stages impeller, single phase 1 HP, 220VAC oil filled motor.
- An unbranded borewell submersible pump, 10 stages, 0.5 HP 220VAC water filled motor, purchased from local market.
- Energy Meter Secure Make, single phase 220VAC 30 Amps, 3200 pulses for 1 KWH unit consumption.
- Power was taken from normal household AC supply
- Water flow and pressure measurement was carried out using conventional simple techniques.
Normal AC power supply was connected to the input of VFD
Output terminals of the VFD were connected to the pump as given in the user guide of the VFD, i.e. U>>Y, V>>R, W>>B
Two different voltage settings were used for testing at 100% and 80% of normal using F00.16 configuration of VFD.
Valve in the delivery line was kept open in such a way as to be near the operating point to get 2.5 to 3.5 bar pressure and around 1800 LPH flow.
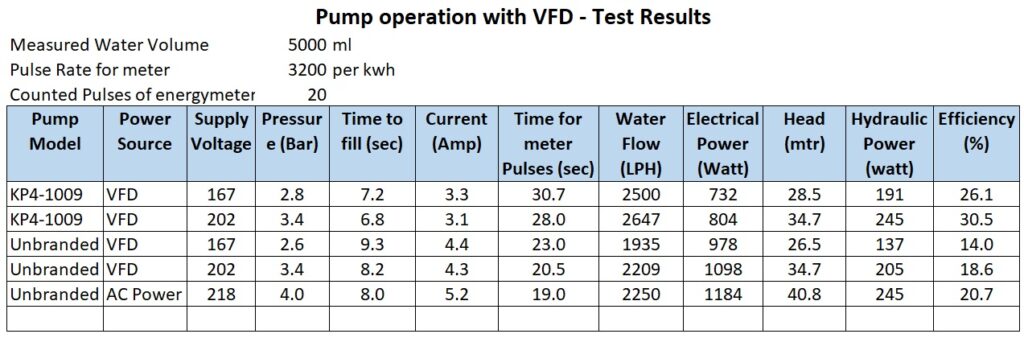
Below are few images and videos related to the tests carried out.
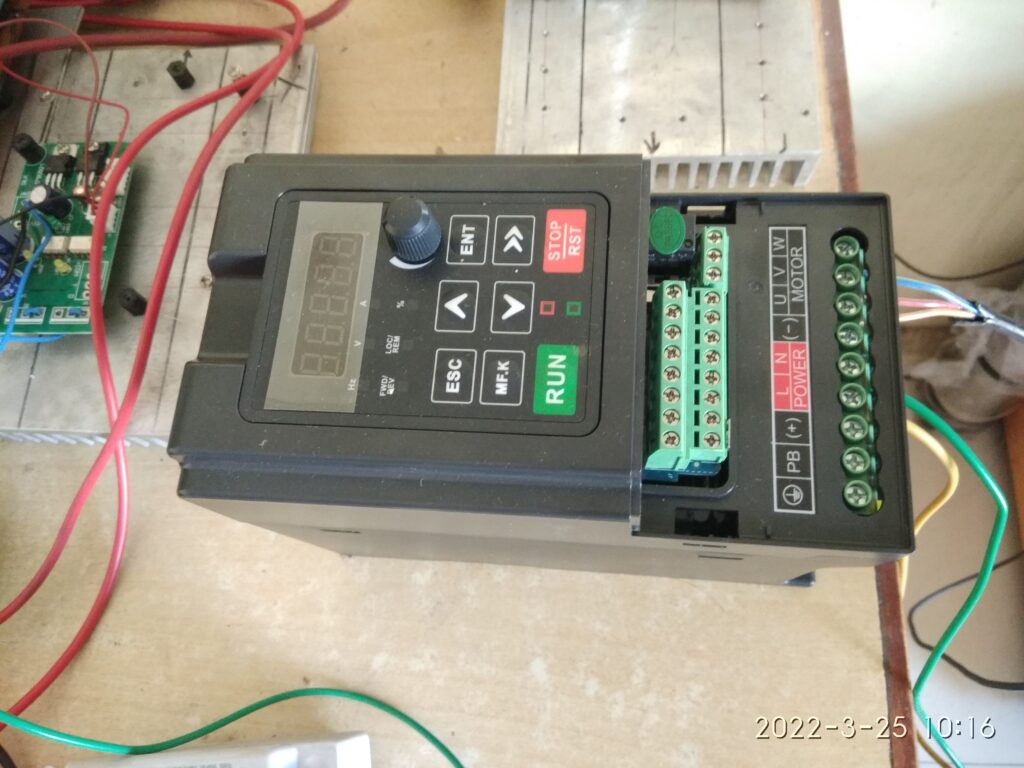
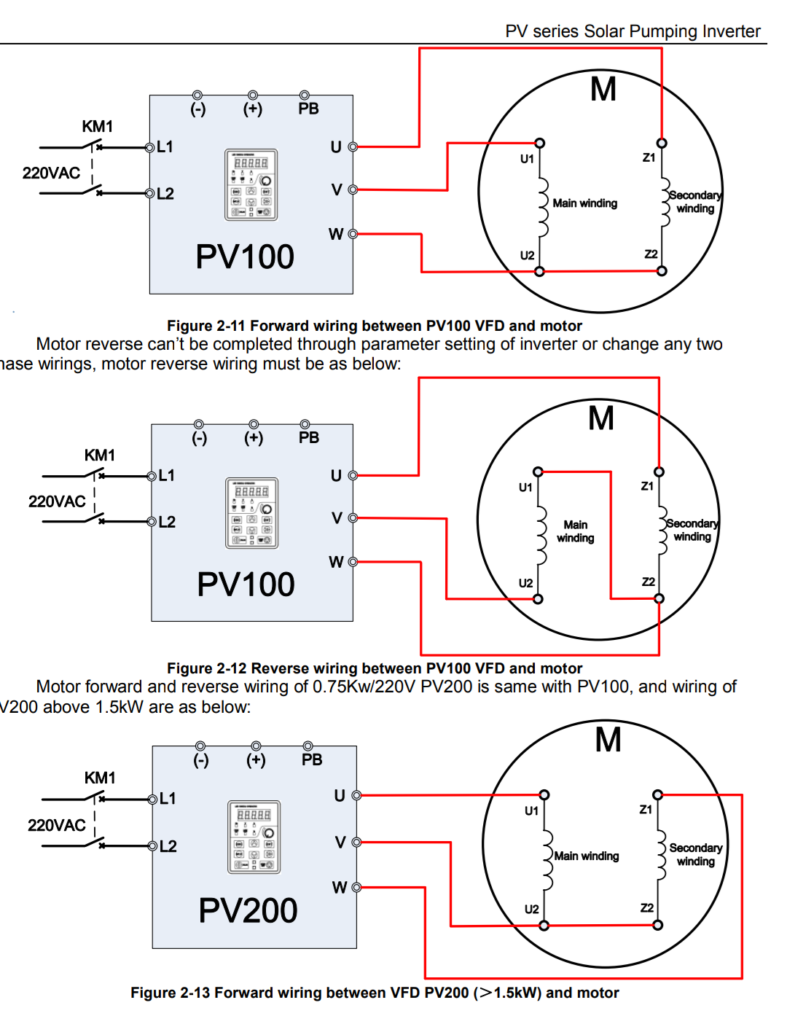
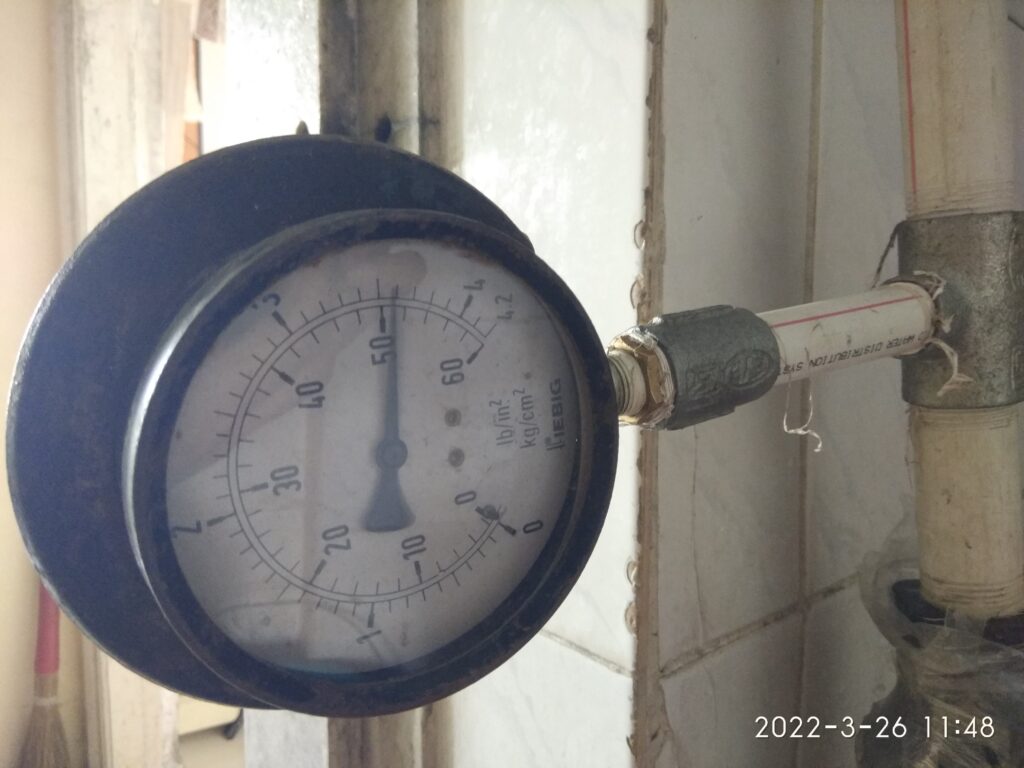
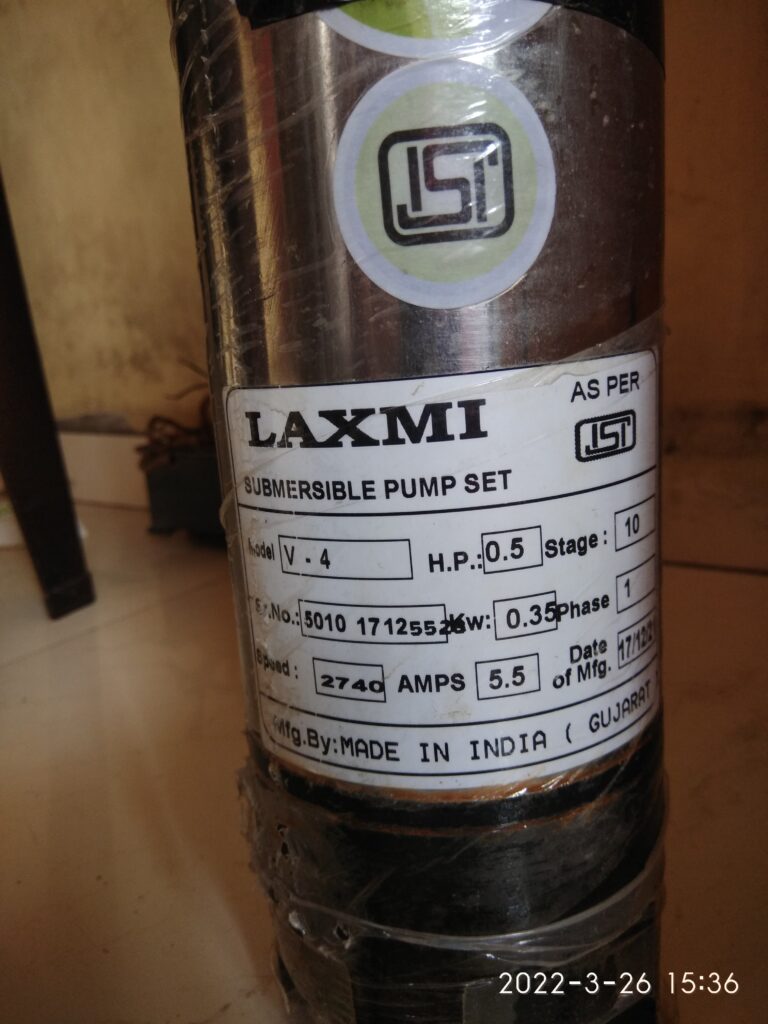
Important observations
The VFD was tried in two different wiring arrangements.
Two wire output mode: This is as per connection F08.00 = 1, whereby the run capacitor of the motor would be kept in circuit and only two wires of the VFD output were connected to the motor starter. In this case it was seen that the motor draws relatively more current untill it starts rotating and there after settles down to normal operating current. The starting current in this case is not as high as it would be otherwise on normal AC power supply, but still higher than running current. This is expected to be so and likely due to the inadequate capacitance at lower starting frequency.
Three wire output mode: This is as per connection F08.00 = 2, as shown in figure 2.11 In this case the motor draws steadily and gradually increasing current until it stabilizes to the normal running current.
This is a very important and useful aspect of the connection arrangement supported by this VFD since it will help deployment of optimum capacity of solar panels.
Further Work
It is essential to carry out similar tests with input power taken from suitably selected solar panels at various time of the day.
An online calculator for panel capacity is presented here at the below link. This will be useful to select the panel ratings for a given pump capacity.
https://www.pbodas.in/solarvfd.php
Update 1
On 30-March-2022 this VFD and 1HP single phase pump was installed at a farm site in Murbad.
Total of 1600 Watt Solar Panels are used to drive the VFD which is a mixed set as below.
8 x 100 Watt 18 V in series with
(
( 4 x 100 Watt 46 V in series )
x 2 such strings in parallel
)
It was seen that pump delivers 3000 to 3600 LPH water at about 30 feet total head, panel side voltage found to be in the order of 300 to 330 VDC, the VFD appropriately keeps regulating the output frequency from 35 to 50 Hz in order to maximize the solar energy generation from the panels and the VFD output voltage was seen to be in range of 160 to 220 VAC.
Long term trial run is planned and results will be published.